BASF Italia
Optymalizacja to kwestia chemii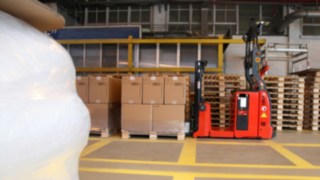
Prosto nie zawsze znaczy banalnie. Dowodem na to może być projekt automatyzacji realizowany przez firmę Linde Material Handling dla BASF Italia. Z myślą o optymalizacji efektywności i bezpieczeństwa dokonano integracji elastycznego, bezpiecznego i szybko wdrażanego rozwiązania dla logistyki 4.0 bazującego na zautomatyzowanych pojazdach.
Jakość na poziomie molekularnym
BASF to przedsiębiorstwo z branży chemicznej zatrudniające na całym świecie 110 000 pracowników, które swoimi produktami zaopatruje niemal wszystkie sektory przemysłu i kraje. We włoskim zakładzie w Pontecchio Marconi są produkowane dodatki do tworzyw sztucznych, a w szczególności stabilizatory świetlne i antyoksydanty.
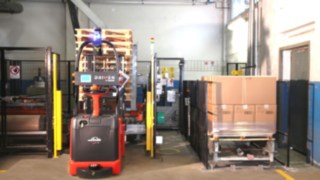
Autonomiczny wózek widłowy Linde podczas pracy w firmie BASF
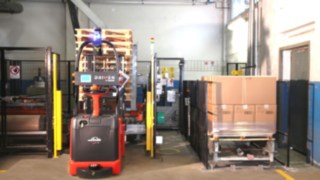
Autonomiczny wózek widłowy Linde podczas pracy w firmie BASF
Zakład w pobliżu Bolonii, w którym praca odbywa się zgodnie z wysokimi standardami dyrektyw bezpieczeństwa (dyrektywa Seveso III), pełni ważną rolę w sieci logistyczno-produkcyjnej firmy BASF. Przedsiębiorstwo to bezpośrednio zaopatruje klientów i magazyny w ponad 50 krajach na całym świecie.
Od problemu do rozwiązania
Centrum procesu produkcyjnego stanowi strefa pakowania. To tutaj trafiają wszystkie materiały wyprodukowane w zakładzie w Pontecchio. W przeszłości transport zapakowanych palet przeznaczonych do tymczasowego składowania w magazynie odbywał się w tradycyjny sposób przy użyciu wózka widłowego prowadzonego przez pracownika.
„Zauważyliśmy, że połączenie jednostki pakującej z magazynem przejściowym było w ten sposób niewydajne. Pracownicy czekali na przygotowanie palet przez maszynę pakującą, aby następnie wózkiem widłowym przetransportować palety do strefy składowania przejściowego. Czasy przestojów między kolejnymi odbiorami były znaczne. Skutkiem tego wykwalifikowani operatorzy byli „blokowani” w czynnościach o niewielkiej wartości dodanej, opowiada Mario Serranti, Kierownik ds. Łańcucha dostaw i Logistyki w BASF.
Z zamiarem znalezienia prostego, ale wydajnego i dopasowanego do naszych potrzeb rozwiązania zwróciliśmy się do firmy Linde.
Mario Serranti, Kierownik ds. Łańcucha dostaw i Logistyki w BASF
Standaryzacja i adaptacja połączone w najlepszy sposób
Firma Linde opracowała dla BASF Italia autonomiczne rozwiązanie, które spełnia rygorystyczne protokoły maksymalnego poziomu bezpieczeństwa w każdym obszarze pracy. Pierwsza analiza bezpieczeństwa w miejscu pracy stała się więc istotną częścią składową projektu. „Gdy rozwiązanie stworzone przez Linde nabrało kształtów, od razu dostrzegliśmy jego potencjał w zakresie automatyzacji, a przede wszystkim bezpieczeństwa”, mówi Mario Serranti.
Rozwiązanie z AGV włączone przez firmę Linde do łańcucha dostaw BASF umożliwia automatyzację czynności o niewielkiej wartości dodanej i optymalizuje poziom bezpieczeństwa. System robotyczny pracuje autonomicznie na ograniczonej przestrzeni bez interakcji z pracownikiem. To innowacyjne rozwiązanie wspiera BASF w realizacji założeń Przemysłu 4.0.
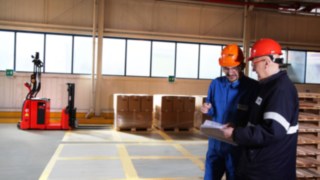
Możliwość konfiguracji najmniejszego detalu
Siłę rozwiązania wdrożonego przez Linde stanowi jego maksymalna konfigurowalność. Dzięki oprogramowaniu monitorującemu włączonemu w infrastrukturę IT klienta standardowe wózki widłowe stają się wózkami „inteligentnymi”. Wózek podnośnikowy komunikuje się bezpośrednio z maszyną pakującą: „w ten sposób system ustawia czasy i prosi pojazd w odpowiednim momencie o usunięcie gotowej palety lub dostarczenie do procesu pustej palety”, wyjaśnia Mario Serranti.
Instalacja nie wymagała żadnych modyfikacji infrastruktury, tylko montażu lasera na wózku widłowym. Jego zadaniem jest pomiar odległości od najważniejszych elementów infrastruktury w magazynie i porównanie ich z mapą obszaru roboczego zapisaną w oprogramowaniu. W ten sposób autonomiczny system Linde może odpowiadać za poruszanie się w realnej przestrzeni, odzwierciedlonej wirtualnie w pamięci wózka widłowego. Przedsięwzięcie poprzedza dokładna analiza, dzięki której okres od prac projektowych do włączenia do normalnej eksploatacji trwa tylko kilka miesięcy.
Wszystkie elementy z myślą o bezpieczeństwie
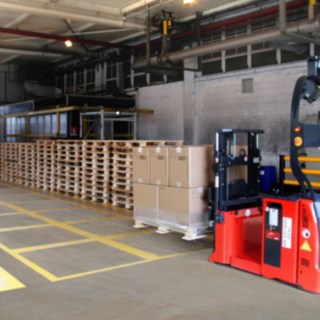
Na pierwszym planie tego projektu znalazło się przede wszystkim zapewnienie i poprawa bezpieczeństwa. Projekt obejmuje wszystkie urządzenia zabezpieczające wymagane przez dyrektywę w sprawie maszyn sterowanych autonomicznie. Po przeprowadzeniu oceny ryzyka wspólnie z klientem w ofercie Linde Robotics uwzględniono wszystkie przepisy obowiązujące w zakładzie.
Wózek podnośnikowy został wyposażony w kilka laserów, które kontrolują otoczenie we wszystkich kierunkach. Laser monitoruje pracę wideł oraz znajdujący się na nich ładunek. Inny laser, skierowany równolegle do powierzchni posadzki, rejestruje przeszkody, przed którymi wózek zatrzymuje się automatycznie. Ponadto wózek jest wyposażony w przycisk zatrzymania awaryjnego, dźwiękową sygnalizację ostrzegawczą i świetlną BlueSpot™ . Taki pakiet urządzeń zabezpieczających zapewnia maksymalne bezpieczeństwo systemu AGV.
Elastyczny projekt
„Zintegrowany projekt pozwala nam bezpośrednio reagować na zmiany. Ogromną zaletą jest przede wszystkim skalowalność. Na rynku globalnym, który podlega nieustannym i gwałtownym zmianom, prognozowanie tendencji średniookresowych przepływów logistycznych i produkcyjnych jest trudne”, wyjaśnia Mario Serranti. Autonomiczne wózki widłowe pracują dziś w BASF na dwie zmiany dzienne. Prędkość można zwiększyć odpowiednio do wzrostu liczby zleceń lub rozszerzyć powierzchnię składowania tymczasowego. Procesy robocze można w każdej chwili skonfigurować na nowo.
Bezpieczeństwo stanowi dla BASF najwyższy priorytet: dzisiaj system FTS pracuje z personelem obsługi bez ryzyka zakłóceń, a wózek widłowy automatycznie i bezkontaktowo zatrzymuje się, gdy zbliża się do niego operator.
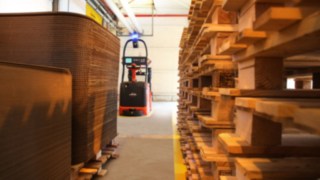
Autonomiczny wózek widłowy Linde transportuje drewniane palety
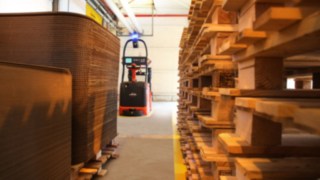
Autonomiczny wózek widłowy Linde transportuje drewniane palety
Ta realizacja to doskonały przykład optymalizacji, polegającej na wdrożeniu w przedsiębiorstwie projektu Przemysłu 4.0: wysoki stopień innowacyjności w prostym, ale niebanalnym systemie, który docenia wartość pracy załogi i zapewnia bezpieczeństwo. System AGV przyczynił się do udoskonalenia procesów pakowania – z korzyścią dla całego zakładu. I tak zaczęła działać chemia optymalizacji.
Elastyczność to wartość o decydującym znaczeniu, w którą należy inwestować.
Mario Serrant, Kierownik ds. Łańcucha dostaw i Logistyki w BASF
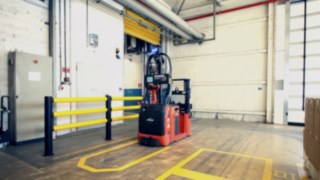