Automatyzacja w ebm-papst
Zmaksymalizowana wydajność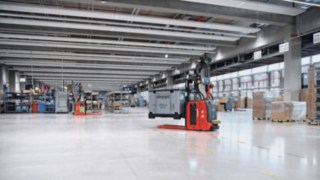
W jaki sposób można udoskonalić dobrą logistykę wysyłkową? Z tym problemem zmagał się specjalista od wentylatorów i silników firmy ebm-papst z Mulfingen, odpowiedzią okazała się pełna automatyzacja ręcznego procesu przepływu materiałów w oparciu o know-how firmy Linde. Realizacja projektu była tak udana, że przekroczono wymaganą wielkość transportu i już planowane są kolejne koncepcje automatyzacji.
„Naturalny przepływ jest z zasady wydajny” - deklaruje Ekspert w dziedzinie wentylacji i technologii napędu, firma ebm-papst, w jednym ze swoich efektownych filmów promocyjnych. Po chwili zastanowienia, nawet laik w dziedzinie fizyki przyzna, że to stwierdzenie ma sens. W końcu dlaczego strumień powietrza miałby samoczynnie wybierać dłuższą drogę? Zamiast tego, jak klarownie widać na przykładzie ponad 20 000 produktów dostarczanych przez tego wiodącego na świecie producenta, może być celowo przekierowany na naszą korzyść: aby chłodzić przeciążone serwery, usuwać niepożądane zapachy z naszych kuchni, utrzymywać żywność na półkach supermarketów w chłodzie, czy zapewniać optymalną wentylację w budynkach. W pewnym sensie zasadę tę można przenieść także na pole intralogistyki. Operator wózka widłowego podejmuje paletę z linii pakującej i przejeżdża z nią bezpośrednio 30 m do punktu odbioru – wiele razy w trakcie zmiany, pięć dni w tygodniu. Proces sam w sobie jest wydajny – ale czy można go jeszcze ulepszyć?
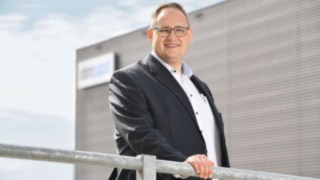
Tobias Arndt, Dyrektor Logistyki w firmie ebm-papst w Mulfingen
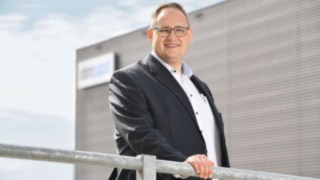
Tobias Arndt, Dyrektor Logistyki w firmie ebm-papst w Mulfingen
„Wkrótce po otwarciu naszego nowego centrum wysyłkowego w Mulfingen-Hollenbach w 2017 roku zaczęliśmy zadawać sobie dokładnie to pytanie” wspomina Tobias Arndt, Dyrektor Logistyki w ebm-papst. W końcu, cały proces zawsze przebiegał tak samo. Ta rodzinna firma od pewnego czasu korzystała ze zautomatyzowanych rozwiązań dla wysoce ustandaryzowanych procesów w swoich zakładach produkcyjnych i magazynie wysokiego składowania. „Wydawało się więc oczywiste, żeby wdrożyć podobne rozwiązanie w naszej logistyce wysyłkowej," opowiada Tobias Arndt. „W ostatecznym rozrachunku bardziej sensowne jest przekierowanie naszych wysoko wykwalifikowanych Operatorów wózków widłowych w inne obszary firmy, do zadań, w których mogą zapewnić większą wartość.” Nie trzeba mieć wykształcenia ekonomicznego, aby zrozumieć logikę stojącą za tym stwierdzeniem.
Kompleksowe rozwiązanie
Szukając odpowiedniej koncepcji automatyzacji, firma ebm-papst, po dobrych doświadczeniach ze sprzętem na wyposażenie działu produkcji, magazynu z wąskimi korytarzami i działu wysyłki, zdecydowała się ostatecznie na partnera sieciowego – firmę Linde MH Hofmann Fördertechnik . Zapytany o początkowe wymagania, Tobias Arndt wyjaśnia: „Rozwiązanie ze statycznym przenośnikiem nie wchodziło dla nas w grę, ponieważ nie chcieliśmy dzielić przejścia przez halę”. Otoczenie linii pakowania 4 i obu punktów przeładunkowych cechuje bowiem duże natężenie ruchu: drogi Operatorów wózków widłowych i pieszych nieustannie przecinają się w trakcie pracy w trybie 3-zmianowym. „Poza tym naszym celem było uniknięcie dużej przebudowy, polegającej na układaniu szyn itp.”, dodaje Ekspert ds. Logistyki. „Klient miał więc dość jasną wizję, czego nie chce”, wspomina Alessandro Zuccala, szef działu Intralogistyki w firmie Hofmann, który nadzorował projekt ebm-papst.
Pierwszym krokiem była analiza faktów i liczb w oparciu o kluczowe parametry docelowe, takie jak wymagana wielkość transportu na godzinę. Alessandro i jego zespół przeszli następnie do etapu weryfikacji koncepcji. Przez kilka dni testowali proponowane rozwiązanie – wózek podnośnikowy Linde L-MATIC .
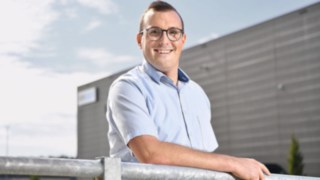
Markus Zink, Kierownik Projektu w firmie ebm-papst w Mulfingen
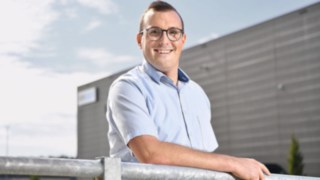
Markus Zink, Kierownik Projektu w firmie ebm-papst w Mulfingen
„Ten etap był dla nas naprawdę ważny”, wyjaśnia Markus Zink, Kierownik Projektu w ebm-papst. „Dzięki temu mogliśmy zobaczyć na własne oczy, że koncepcja działa nie tylko na papierze lub w innych firmach, ale też w naszej hali wysyłkowej.” W tym celu Inżynierowie ds. wdrożeń firmy Hofmann stworzyli najpierw cyfrową mapę warunków panujących w magazynie, która stanowiła podstawę orientacji wózka Linde L-MATIC w określonych stałych punktach, i żadna dodatkowa infrastruktura, jak np. reflektory itp. nie była wymagana. Takie rozwiązanie jest praktyczne, ponieważ pozwala w łatwy sposób dostosować trasy przejazdu na późniejszym etapie, w przypadku zmiany warunków ramowych. Etap weryfikacji koncepcji obejmował również testy z ponad 20 różnymi nośnikami ładunku używanymi na linii pakującej nr 4. „Niektóre wentylatory i silniki muszą być przetransportowane z linii pakowania do punktu przeładunkowego magazynu wysokiego składowania, a inne do punktu odbioru wysyłki bezpośredniej”, wyjaśnia Kierownik Projektu Markus Zink. „Oczywiście, nasze rozwiązanie musiało być odpowiednie dla obu tych przypadków użycia”, uzupełnia Ekspert firmy Hofmann Alessandro Zuccala. Aby tak się stało, firma Hofmann-Fördertechnik podjęła się złożonego zadania zaprogramowania wózków podnośnikowych Linde L-MATIC. Za pośrednictwem sieci firmowej ebm-papst wózki Linde zostały włączone do wewnętrznego systemu SAP Extended Warehouse Management (EWM). Markus Zink był pod wielkim wrażeniem: „To było fantastyczne, że nasz partner sieciowy Linde zajął się wszystkim – planowaniem, sprzętem i wymaganiami dotyczącymi oprogramowania”.
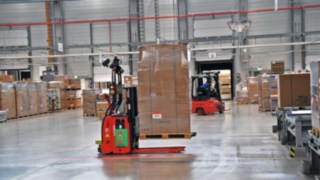
Automatyzacja z bezproblemową integracją
Od marca 2020 roku łącznie trzy wózki Linde L-MATIC pracują w ebm-papst, odbierają palety z przenośnika taśmowego i transportują je do odpowiedniego punktu odbioru – z ekstremalnie wysoką wydajnością i bez konieczności wsparcia ze strony człowieka. „Zlecenia są przekazywane przez nasz system SAP EWM bezpośrednio do wózków, zanim paczka znajdzie się na końcu linii pakowania – tak, aby wózki mogły być na miejscu na czas”, wyjaśnia szef projektu Markus Zink. Gdy wózki są w ruchu, po obu ich stronach świeci wyraźny czerwony pasek ostrzegawczy LED. Są one również wyposażone w Linde TruckSpot™ projektor, który podczas cofania wyświetla duży trójkąt ostrzegawczy na podłodze hali. Markus Zink podkreśla znaczenie tych funkcji: „Bezpieczeństwo musiało być naszym najwyższym priorytetem, ponieważ wózki pracują obok innych pieszych i operatorów wózków widłowych”. Z tego właśnie powodu wózki Linde L-MATIC zostały również połączone sieciowo z osobno zamontowaną skrzynką komunikacyjną, która w przypadku pożaru w hali wysyła sygnał bezpośrednio do wózków i zatrzymuje je w pozycji, w której nie blokują żadnych dróg ewakuacyjnych ani nie utrudniają pracy służbom ratunkowym.
Ładowanie urządzeń z bateriami litowo-tlenkowo-tytanowymi (LTO) przebiega z taką samą łatwością jak współpraca z ludźmi. Markus Zink wyjaśnia: „Firma Hofmann zainstalowała nową stację ładowania z ruchomymi stykami, do której pojazdy Linde L-MATIC mogą dokować automatycznie, na przykład w przerwach między zmianami. Dzięki temu bez problemu radzimy sobie z tymi trzema wózkami na wszystkich zmianach – nawet w najbardziej intensywnych momentach”. A jeśli któreś urządzenie się zepsuje, „nasz zespół jest gotowy do pomocy”, potwierdza Alessandro Zuccala z firmy Hofmann. Dzięki możliwości zdalnego serwisu specjalista Hofmann może połączyć się z urządzeniem i w łatwy sposób pomóc w razie problemów z oprogramowaniem, bez konieczności wzywania ekspertów zewnętrznych. „To duża zaleta”, bilansuje Tobias Arndt, Kierownik Logistyki w ebm-papst. A skoro mowa o zaletach: jest nią również to, że wózki L-MATIC znacznie przekraczają pierwotnie wymaganą wydajność 36 przejazdów na godzinę, osiągając w godzinach szczytu nawet 50 przejazdów i zapewniając dyspozycyjność na poziomie niemal 100%. Tobias Arndt: „To się nazywa wydajność!”
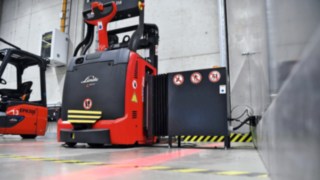
ebm-papst Mulfingen GmbH & Co. KG
Firma ebm-papst Mulfingen GmbH & Co. została założona w 1963 roku i od tego czasu stała się wiodącym na świecie producentem wentylatorów i silników napędowych. Z 29 oddziałów produkcyjnych i 48 oddziałów dystrybucyjnych na całym świecie, ta firma rodzinna dostarcza klientom z różnych branż skrojone na miarę i energooszczędne rozwiązania – od kompaktowych, osiowych i odśrodkowych wentylatorów po dmuchawy, pompy i kompletne systemy napędowe. Zadania logistyczne w zakładzie głównym w Mulfingen, ebm-papst powierza technologii i wiedzy firmy Linde Material Handling oraz partnerowi sieciowemu Linde – firmie Hofmann Fördertechnik. Ze względu na duży sukces projektu automatyzacji zainicjowanego w latach 2018/2019, firma planuje obecnie automatyzację licznych kolejnych zadań transportowych na miejscu, dzieląc się doświadczeniami z innymi oddziałami niemieckimi w Landshut i w St. Georgen.