Heidelberger Druckmaschinen AG
Nowoczesna logistyka w Heidelbergu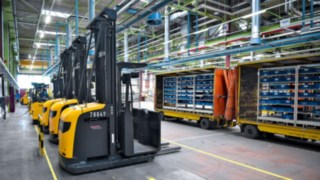
W czasach coraz bardziej zindywidualizowanych wymagań klientów również intralogistyka musi się dostosowywać do zmieniających się warunków produkcyjnych. Przykład firmy Heidelberger Druckmaschinen AG (Heidelberg) z siedzibą w Wiesloch/Walldorf pokazuje, w jaki sposób odbywa się to w przedsiębiorstwie przemysłowym działającym na skale światową. Wraz z firmą Linde Material Handling i jej partnerem Suffel Fördertechnik (będącym generalnym wykonawcą zlecenia) wdrożono całkowicie nową koncepcję logistyczną optymalizującą dostawy materiałów na linię montażową offsetowych maszyn drukarskich.
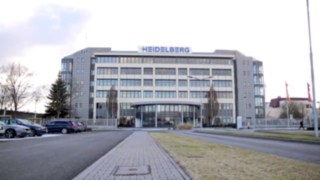
Jaskrawe opakowanie płatków kukurydzianych na stole śniadaniowym, modny magazyn na błyszczącym papierze czytany w przerwie na kawę lub elegancka wizytówka podczas lunchu biznesowego: chociaż nasz nowoczesny świat staje się coraz bardziej cyfrowy, nadal prawie na każdym kroku mamy do czynienia z materiałami drukowanymi. Niezależnie od ich różnorodności prawdopodobieństwo, że zostały wyprodukowane na Speedmasterze z firmy Heidelberg, jest dość wysokie. To znane na całym świecie przedsiębiorstwo, które zatrudnia 11 500 pracowników, zalicza się do czołowych graczy w swojej branży. Firma ma swoją siedzibę miejscowości Wiesloch/Walldorf w Badenii-Wirtembergii, w centrum silnego gospodarczo niemieckiego regionu Rhein-Neckar. Firma Heidelberg posiada tutaj największą i najnowocześniejszą fabrykę maszyn drukarskich na świecie: na powierzchni kilometra kwadratowego produkowane są między innymi wiodące na rynku arkuszowe maszyny offsetowe obsługujące różne formaty papieru.
Nowe wyzwania –
Nowe Koncepcje
Firma Heidelberg od wielu lat obserwuje ciągłą zmianę w kierunku większej indywidualności w zakresie wymagań klientów: Wcześniej w każdym zakładzie budowaliśmy przeważnie podobne maszyny drukarskie – wspomina Dyrektor Działu Logistyki Zakładu Matthias Ehmler. Teraz często produkujemy systemy dostosowane do potrzeb klienta i z tego powodu nastąpił gwałtowny wzrost liczby różnych wersji – wyjaśnia.
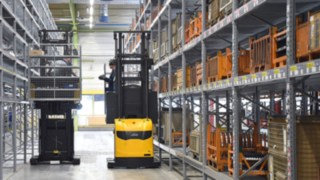
Wózki typu reach truck (wysokiego składowania) i wózki do komisjonowania od firmy Linde w magazynie Heidelberger Druckmaschinen
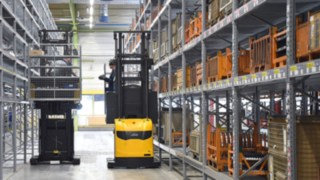
Wózki typu reach truck (wysokiego składowania) i wózki do komisjonowania od firmy Linde w magazynie Heidelberger Druckmaschinen
Ten trend ostatecznie wpływa również na linie montażowe: Pracownicy na stanowiskach montażowych coraz częściej przemieszczali się pomiędzy niedającymi się zarządzać „górami materiałów”. Im większa różnorodność, tym więcej pojemników na części było potrzebnych. Miało to coraz bardziej negatywny wpływ na wydajność pracowników – wyjaśnia Ehmler. W rezultacie dwa lata temu rozpoczęliśmy projekt reorganizacji działu montażu. Chcieliśmy efektywniej wykorzystać obszary produkcyjne i dostarczyć materiał do pracownika, a nie na odwrót.
Restrukturyzacji działu montażu w kierunku konstrukcji modułowej towarzyszyła reorganizacja intralogistyki w hali o długości 600 metrów. W przyszłości materiały o niskim zapotrzebowaniu dziennym nie będą już dostarczane w kontenerach, lecz będą zamawiane, pobierane, a następnie wprowadzane na linie montażowe przez pociągi. W tym celu w przedniej części hali montażowej utworzono centralny obszar kompletacji i konsolidacji zamówień z wysokimi regałami.
Naszym celem było zapewnienie bezpiecznych, wydajnych i elastycznych dostaw materiałów przy jak najlepszym wykorzystaniu dostępnej przestrzeni – wyjaśnia Dyrektor Logistyki fabryki Heidelberger. Oto ambitny projekt, którego realizacja w trakcie bieżącej eksploatacji wymagała doskonałego zazębiania się różnych procesów.
Kompetentny partner poszukiwany
Faza przetargowa rozpoczęła się od ogromnego spisu wymagań. Szukaliśmy partnera, który zrealizowałby budowę regałów i dostawę wózków włącznie z systemem do zarządzania flotą w formie generalnego wykonawstwa – Ehmler nakreśla plan zadań przeznaczonych dla wybranego przedsiębiorstwa działającego w branży logistyki magazynowej. Jednocześnie należało oczywiście przestrzegać uzgodnionego z nami harmonogramu czasowo-kosztowego, tak abyśmy mogli skupić się całkowicie na zarządzaniu podstawowymi danymi i szkoleniu pracowników. Wiele aspektów przyczyniło się do tego, że zlecenie otrzymała ostatecznie firma Linde Material Handling jako producent i dostawca odpowiednich rozwiązań oraz jej partner Suffel Fördertechnik: Po pierwsze, sprzęt Linde zaimponował nam swoimi unikalnymi cechami technicznymi. Po drugie, byliśmy pod wrażeniem doradztwa i warunków umowy – przyznaje Ehmler.
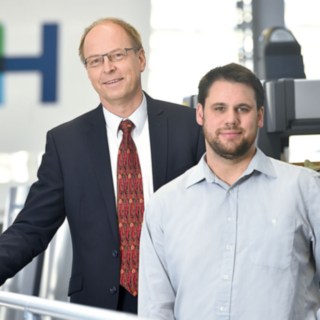
Budowa regałów i dostarczenie wózków przez jednego dostawcę sprawdziło się w naszym przypadku pod każdym względem.
Matthias Ehmler, Dyrektor Działu Logistyki w firmie Heidelberg
Aby umożliwić dostarczenie na linię montażową części do danego zlecenia należało najpierw znaleźć odpowiednie rozwiązanie dla magazynu do komisjonowania, a tym samym dla kluczowego punktu nowej koncepcji logistycznej. W spisie wymagań zamieściliśmy już pewne pomysły i zalecenia. W trakcie realizacji były one sukcesywnie omawiane z firmami Linde i Suffel. W magazynie do komisjonowania miało znaleźć się miejsce na przechowywanie zarówno dużych, jak i małych elementów, całych podzespołów, a także pojemników o różnych kształtach i wymiarach. Miał on również spełniać wysokie standardy w zakresie bezpieczeństwa pracy – Stefan Heger, Project Manager, opowiada o największych wyzwaniach.
Dobrze zorganizowany supermarket
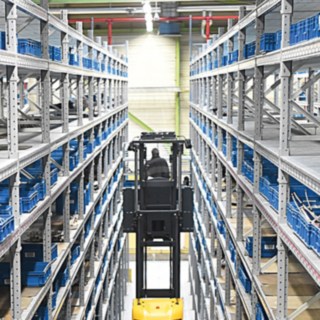
Nowy magazyn wysokiego składowania zbudowany z 13 rzędów regałów i obejmujący 4500 numerów artykułów działa jak supermarket i składa się ze strefy szerokiego przejścia o szerokości 4,05 metra oraz strefy z trzema wąskimi korytarzami. W szerokim przejściu pracują 3 wózki wysokiego składowania (reach trucki) Linde R14, które przyjmują towary do magazynu. W wąskich korytarzach 7 wózków do pionowego komisjonowania Linde V przejmuje na siebie zadania komisjonowania oraz uzupełniania zapasów. Wyposażenie magazynu pochodzi z trzech różnych źródeł. Pojemniki na duże ładunki docierają przez łącznik pomostowy z sąsiedniego centralnego magazynu zaopatrzenia powierzchni komisjonowania. Pojemniki na małe ładunki są zbierane wstępnie w odrębnym automatycznym magazynie małych części i dostarczane za pośrednictwem wewnętrznego systemu transportowego. Kompletacja jest wykonywana w strefie montażu wstępnego, która jest połączona ze strefą komisjonowania.
Ważną rolę odgrywa ergonomia i bezpieczeństwo
Komisjonowanie w magazynie wysokiego składowania odbywa się wyłącznie za pomocą modułowych wózków do pionowego komisjonowania Linde V. Pracownik znajdujący się w wózku pobiera potrzebny materiał z półek na wysokości do 6,5 metra.
Rozwiązaniem ułatwiającym pracownikowi sięganie w głąb regału z wózka V są bariery przechylne. Ta opcja wyposażenia to wielka zaleta Linde, która może doskonale sprawdzić się w naszym nowym magazynie wysokiego składowania – podkreśla Jens Kernbach, Dyrektor Hall Logistics w firmie Heidelberg. W Heidelbergu czujemy się odpowiedzialni za naszych pracowników.
Aby proces komisjonowania mógł przebiegać w sposób całkowicie bezproblemowy, urządzenia poruszają się w korytarzach magazynu na zasadzie indukcji. Dzięki temu operator może całkowicie skoncentrować się na procesie obsługi towaru i przejeżdża w optymalnej odległości od regału. Do wyposażenia wózka należy też asystent do bezpiecznej nawigacji w wąskich korytarzach (Aisle Safety Assistant, ASA), który w razie potrzeby zatrzymuje wózek.
Możemy teraz wykluczyć uszkodzenia regałów i urządzeń – cieszy się Heger, Project Manager. Ponadto wejścia do magazynu zostały zabezpieczone barierami świetlnymi. Gdy osoba nieupoważniona wchodzi do strefy przeznaczonej wyłącznie dla wózków, rozlega się alarm. W urządzeniach została też wstępnie zainstalowana półautomatyczna nawigacja laserowa firmy Linde, która posiada możliwość dalszej optymalizacji. Za pomocą tego rozwiązania (opartego na technologii RFID) wózki do pionowego komisjonowania nawigują do zaprogramowanego miejsca bez pomocy operatora.
Dzięki indukcyjnemu prowadzeniu możemy wykluczyć uszkodzenia regałów i samych wózków.
Stefan Heger, Project Manager w firmie Heidelberg
Elastyczne i niewymagające dużej ilości miejsca
Łącznie 3 pociągi Linde (Linde Load Trains) przewożą składy ze stacji transferowej do pracowników na liniach produkcyjnych. W skład pociągu logistycznego wchodzi ciągnik Linde P50 oraz doczepione do niego jeden lub dwa wagoniki. Każdy moduł umożliwia jednoczesny transport dwóch wózków zestawowych, które ze względu na brak środkowej osi można zakładać lub zdejmować z obu stron. Pozwala nam to na elastyczne rozplanowanie odcinków tras – mówi Stefan Heger. Kolejną zaletą jest mała ilość miejsca, jakiej potrzebują pociągi Linde Load Train, które precyzyjnie poruszają się po alei o szerokości 2,2 metra.
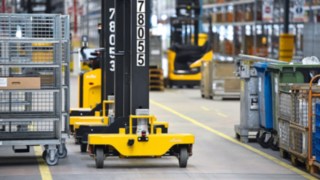
Bilans jest pozytywny, a optymalizacja postępuje
Również po zakończeniu inwestycji Matthias Ehmler szuka dalszych możliwości optymalizacyjnych. Z pomocą przyjdzie mu między innymi moduł „Analiza użytkowa” w systemie zarządzania flotą od firmy Linde. Ehmler mówi: Już od wielu lat korzystamy z oprogramowania connect:, aby kontrolować dostęp do wózków i rejestrować zdarzenia. Mamy na tym polu wiele dobrych doświadczeń. Teraz możemy również wykorzystywać oprogramowanie do optymalizacji naszych procesów i, na przykład, do dalszego zwiększania wykorzystania sprzętu.
Minął już prawie rok od czasu, gdy w Heidelbergu wdrożono nową koncepcję logistyki magazynowej zgodnie z zasadą działania magazynu wysokiego składowania oraz z użyciem wózków do pionowego komisjonowania, reach trucków i pociągów logistycznych. Konkluzja Matthiasa Ehmlera jest bardzo pozytywna: Zrealizowaliśmy projekt nie tylko w zaplanowanych ramach czasowych i budżetowych, ale też osiągnęliśmy nasz cel: optymalną logistykę. Firmy Linde i Suffel świetnie się spisały.
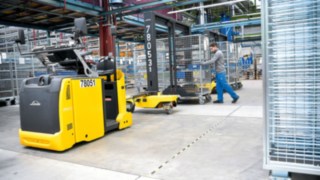